Production planning is one of the crucial steps in the manufacturing process, irrespective of the industry or company size. It normally involves allocation of resources, employees, materials and production capacities in order to satisfy customers needs and produce a set number of items.
However, manufacturers often face various difficulties in the planning process. This is especially typical when scaling up production facilities. When a company outgrows the startup phase and is transforming to a medium-sized business, it’s getting evident that previous management and planning approaches don't work well anymore.
So let’s have a look at some of the challenges manufacturers might face when it comes to the changes in production planning and how to deal with them.
A single-manager approach to planning
In small production companies, the production plan is usually managed by a single employee. This incurs additional business risks since the company’s production process to a significant extent depends on that one person. Besides, if a production planning manager is the only employee who is well familiar with the production plan or even has access to it, the company may face serious problems in case of his or her sick leave or quitting the job.
Implementing an ERP system with the production planning features and flexible access rights management can help integrate data flows and make sure your planning activities are transparent and easily accessible to all the parties concerned. You no longer depend on a single employee’s personal records or database since all the data is available in the system.
Manual planning
While the company is small, it may be efficient to rely on manual planning and using tools like Excel. But as the business grows, the number of production orders increases and manual planning becomes ineffective. The number of mistakes caused by manual labor skyrockets, additional costs arise.
For example, if an order is modified or canceled, you’ll need to quickly adjust the production plan – which becomes quite a challenge when handled manually since you have to change data simultaneously in numerous Excel sheets. This makes errors almost inevitable. Another example is the hardship of balancing the number of orders and the production volumes so that there’s no product surplus on the one hand or shortage on the other. When trying to calculate this manually, there’s always a danger of overlooking some crucial factors or numbers.
To deal with this problem, manufacturers can consider automating the planning process, at least partly, by implementing automation scripts and software integrations. Alternatively, they can consider adopting an all-in-one resources management tool. A unified management and accounting system can help enhance the planning process and eliminate mistakes by tapping into the real-time data on orders, stock, sales, and finances.
Estimating production lead time
Another hardship caused by the lack of automation is that it does not allow manufacturers to effectively plan the production lifecycle at the moment when the order is received. The estimation process includes too many variables, so, when calculated manually, the actual shipment may take longer than the customer expects.
Besides, for bigger companies, different departments can have a hard time syncing the overall schedules and deadlines. Often, they end up producing something that is no longer needed since the deadline wasn’t met and the client has already left. All this predictably results in financial losses and customer churn.
So, efficient coordination and intelligent resource management are crucial when it comes to planning the production lead time.
How 1C:Drive helps deal with these issues
1C:Drive provides all the necessary tools for effective production planning, including scheduling, data tracking, full control of equipment, materials and components availability as well as subcontractors management when outsourcing certain tasks.
This is essentially an all-in-one solution that will help curtail the mess of manual labor and automate the planning process, allowing for greater transparency and efficiency.
As a result, you’ll be able to make more informed decisions, estimate production time with greater precision, and better meet clients’ expectations.
How to Plan Production of Order in 1C:Drive ERP
How to Use Materials Planning in 1C:Drive ERP
How to Manage Bills of Materials (BOM) in 1C:Drive ERP
How ERP Systems Help Tackle Ineffective Production Planning
25.04.2024, 11:09
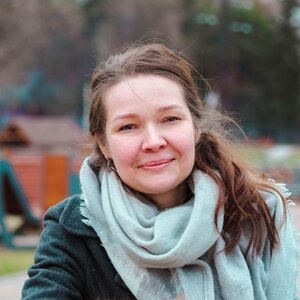
Ekaterina Kopnysheva
1Ci Product Marketing Manager